sheet metal minimum flange length We’ve broken down our minimum bend radii into two values: minimum hole distance and minimum flange distance. Minimum hole distance specifies how far a hole must be placed from . IP68 Waterproof Universal 12V 24VDC Metal Case Digital Wired Keypad for Garage Door, Gate Opener and Access Control Systems
0 · sheet metal minimum bend length
1 · sheet metal bending radius chart
2 · sheet metal bending design guidelines
3 · sheet metal bending chart
4 · sheet metal bend deduction chart
5 · minimum sheet metal hamtramck radius
6 · maximum thickness sheet metal bending
7 · distance of hole from edge sheet metal
Surface metal raceway allows you to add fixtures and outlets without disturbing the drywall, plaster or insulation in your home. It is also ideal for adding wire when you can't go into the .
We’ve broken down our minimum bend radii into two values: minimum hole distance and minimum flange distance. Minimum hole distance specifies how far a hole must be placed from .

metal house lanterns
The minimum recommended sheet metal flange bend length avoid cracks in the bending area. It shall be equal to three times of sheet thickness plus bend radius. Minimum Sheet Metal .Minimum flange length on sheet metal parts must be at least 4 times the material thickness. It is recommended to use the same radii across all bends, and flange length must be at least 4 . Learn how to calculate the minimum bending edge for sheet metal with our step-by-step guide. Get expert tips and ensure precise results in your .
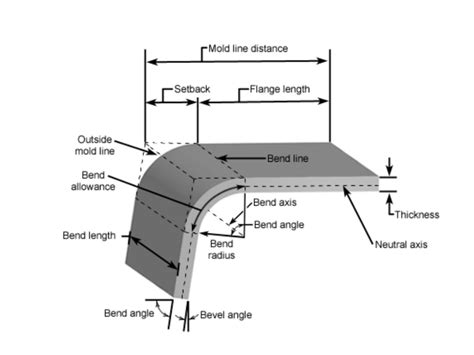
sheet metal minimum bend length
Brake press operators should know the minimum flange lengths for their tooling before attempting bends that may not work and while it is possible to calculate the minimum flange having an Air Bend Force Chart on hand certainly makes it . The bending force table below helps you identify the minimum flange length b (mm) and inside radii ir (mm) according to material thickness t (mm). You can also see the die width V (mm) that is needed for such .
What is the minimum flange width for sheet metal? Factors like material thickness, bend radius, and application requirements typically determine minimum flange heights for sheet metal. In general, the flange height should be at least .Minimum Flange Lengths. The minimum flange length is the minimum length of the straight section of material between the bend and the edge of the sheet. It's crucial to check and meet . This article explores the essential formulas and guidelines for determining the minimum and maximum bending dimensions, ensuring precision in your metalworking projects. By understanding these calculations, you can .What is the minimum required Flange Length in Sheet metal Bending? The minimum flange length shall be equal to 4 times the sheet thickness plus the inside radius. Minimum Flange length = 4 X T (sheet thickness) + R (Inside .
sheet metal bending radius chart
sheet metal bending design guidelines
First, bend charts list a minimum flange length, but is there a formula that can be used for a minimum dimension as it relates to the overall feature length to prevent distortion in holes, for example? . I have presented .

Bend deduction and flat length Calculate K factor and bend allowance for sheet metal bending Calculate length and weight of a sheet metal coil Calculate radiused bump bending Shearing force calculator Sheet metal bending parameters calculator . V-die opening and minimum flange. You just have to insert the characteristics of the sheet metal to .
A zero flange would require stamping, there is no folder/bender that will give you a zero flange thickness. Have a chat to the person manufacturing. Most press brakes work on a 6 - 8 time time V size to the material thickness. i.e 3mm plate needs a 18mmV - 24mmV size optimally which gives you a 9 - 12mm flange inside the bend.
Sheet metal bending can be done using many methods. We discuss those along with springback, bend allowances, k factor, design tips etc. . I can now see that the minimum flange length is 8.5 mm for such a bend, so I have to keep it in mind when designing. The required die width is 12 mm and tonnage per meter is 22. The lowest common bench .Determining minimum flange length is an important step in any successful bending operation. WILA recommends a flange length that is at least 6 times the material thickness. . For more information about bending short flanges or any other type of sheet metal bending on a press brake, just give us a call. We'll be happy to answer any questions .The minimum flange length is the minimum length of the straight section of material between the bend and the edge of the sheet. It's crucial to check and meet the minimum flange length requirements specified for the material and thickness being used. Refer to the material table above for the minimum flange lengths for each material and thickness. Ever wondered how to calculate the bending limits of sheet metal accurately? This article explores the essential formulas and guidelines for determining the minimum and maximum bending dimensions, ensuring precision in your metalworking projects. . The minimum flange size, “l min “, for various material thicknesses is listed in Table 5 .
Sheet metal parts are used all over and are great for enclosures and housings. 1 vin mostbet casino pin up casino lucky jet kz. HLH Prototypes, Custom Prototype Manufacturing; About. . The minimum flange length which can be applied to parts is also dictated by the die opening, a good rule to follow is to allow for at least 4 times the .Window bends are allowed up to 90° for sheet metal and polycarbonate parts. More acute angles require review by our team. Learn about our window bend design requirements. Joggle bends are allowed up to 90° for sheet metal parts only. You can find the minimum and maximum joggle flange values on the specification charts for your chosen material.
Minimum Flange Dimensions Minimum Flange Length Minimum Overall Dimension. . Per our bending design guidelines, we cannot form u-channel or c-channel type beds with a base-to-flange ratio smaller than 2:1 in sheet metal. On your flat pattern, you can use whichever of the dimension tools you prefer in QCAD to check this: When it comes to distortion, the question is whether the flange meets our minimum length requirement for the material across the entire bend.. You can find both the Min Flange Length (Before Bend/Flat Pattern) and Min Flange Length (After Bend) values in the Material Details.. If you are working in a 2D program like QCAD to design your part, refer to the Min .
The Importance of Flange Size in Sheet Metal Bending. . For example, 0.250” stainless steel has a minimum flange length of 1.150″ before the bend, while a much thinner 0.040” aluminum sheet can be bent with a flange as short as 0.255″. Fig.: Bending specs for 0.250” 304 Stainless. The Material Details for each can be found at the .Recommended Minimum Flange Length and Inner Radius. Metal folding chart. According to every sheet thickness, there’s a suitable inner radius and flange length when bending sheet metal. It is visibly clear that it is not possible to bend the part on the right. The flange is too short.CONIC TECHNICAL GUIDE vol.13 BENDING FAQ 1 (TOOL INTERFERENCE, MINIMUM FLANGE LENGTH) TECHNICAL GUIDE. PRESS BRAKE TOOLS. . There is a method of verifying the “press brake tool cross-sectional shape .
SCS specifies that 1.2MM steel needs a bend radius of .024MM minimum. Additionally, your initial bend could be considered a "joggle" as it changes direction rapidly with little extension to the flange length. SCS specifies that for all U or C bends, the flange length must be a minimum of 2X the base length.
sheet metal bending chart
Sheet Metal Flat Length can be calculated with this calculator. This calculator can be used for number of bends up-to 5. It is recommended to calculate K factor value first. . This calculator can be used for calculating sheet metal design parameters such as inside bend radius, minimum flange length, slot to edge distance etc .Hems are used to create folds in sheet metal in order to stiffen edges and create an edge safe to touch. For tear drop hems, the inside diameter should be equal to the material thickness. . Distance from outside mold line to the bottom of the cutout should be equal to the minimum flange length prescribed by the air bend force chart. Required bending force to bend metal sheet of 1 meter length; V-opening width; Minimum flange length. How to Select the Most Appropriate V-Opening? The V-opening refers to the distance across the lower die mouth, and the appropriate V-opening of the die should be selected according to the sheet metal thickness. The air bending chart above shows . The minimum flange a given V die can form is approximately 77 percent of its opening. So a part being formed over a 1.-in. V die will need at least a 0.77-in. flange. Many sheet metal designers like to save metal and specify a flange that’s too short, like a 0.5-in. flange in 0.125-in. material thickness (see Figure 4). According to the rule .
The minimum flange a given V die can form is approximately 77 percent of its opening. So a part being formed over a 1.-in. V die will need at least a 0.77-in. flange. Many sheet metal designers like to save metal and specify a flange that’s too short, like a 0.5-in. flange in 0.125-in. material thickness (see Figure 4). According to the rule .
Our online calculator allows you to determine sheet metal bending parameters within seconds accurately. Enter your project data and instantly get tonnage, inner radius and minimum edge. Die opening. The die opening is usually chosen according to the thickness of the sheet metal, with this rule: Thickness < 6 mm die opening = thickness × 8Sheet metal parts would cost 2-4x more if perfect accuracy was the standard. As such, only expect the raw laser cut part to be accurate. . Most shops can make quite precise sheet metal parts if you follow some guidelines about radii and flange length in relation to the material and material thickness. You . talk to your shop about minimum .used to calculate the minimum distance required: For a hole < 1" in diameter the minimum distance "D" = 2T + R (see fig. "B") For a slot or hole > 1" diameter then the minimum distance "D" = 2.5T + R (see fig. "C") Form height to thickness ratio – To determine the minimum form height for sheet metal use the
Flange Length. In a bent sheet metal part, the flange length is the distance from where the punch bends the metal, to the edge of the part, or to the next major feature like another bend. In an air bending operation in particular, the amount of flange area left open matters a great deal. If there is not enough flange on both sides of the bend . The second flat-blank-development example adds the two dimensions (from edge to the apex), and subtracts a bend deduction. In this case, the calculations use a complementary angle for the OSSB, and the dimensions are called from the edge to the apex—again, as specified in Figure 4.. Outside Setback (OSSB) Our basic guidelines for sheet metal fabrication include important design considerations to help improve part manufacturability, enhance cosmetic appearance, and reduce overall production time. . Size Maximum Dimensions SIZE 1,193.8mm x 3,022.6mm LENGTH 3.048m Minimum Dimensions FLAT PART 12.7mm x 12.7mm FORMED PART 38.1mm x .
sheet metal bend deduction chart
I want to replace a 30A breaker with a 20A breaker at the panel. At the moment there is a small bit of 10/2 wire (12 inches long) that goes into a relay box and from that relay box comes 12/2 wire powering 4250W baseboards at 240v = 17.7A. This is probably safe but not necessarily to code.
sheet metal minimum flange length|distance of hole from edge sheet metal